Background
To enable AnQore to deliver on their mission we realized that we need to be able to constantly monitor the location, speed and safety performance of all our rail, road and container equipment and its content. We started a fundamental improvement project involving the entire organisation with the objective to enable AnQore to always deliver safely and securely, day in, day out.
The initial focus of the project was safety and our focus was aimed at the following topics:
- Human interface: speeding of trains and trucks, and handling of equipment;
- Technical state of the equipment, detection of: shocks, wear and tear of wheel sets, and leakages;
- Esurance of compliance to legislation: track speed limits, Basisnet regulation, other regulations;
- Minimize the effects of an incident: Speed of emergency response communication, help contain product spills
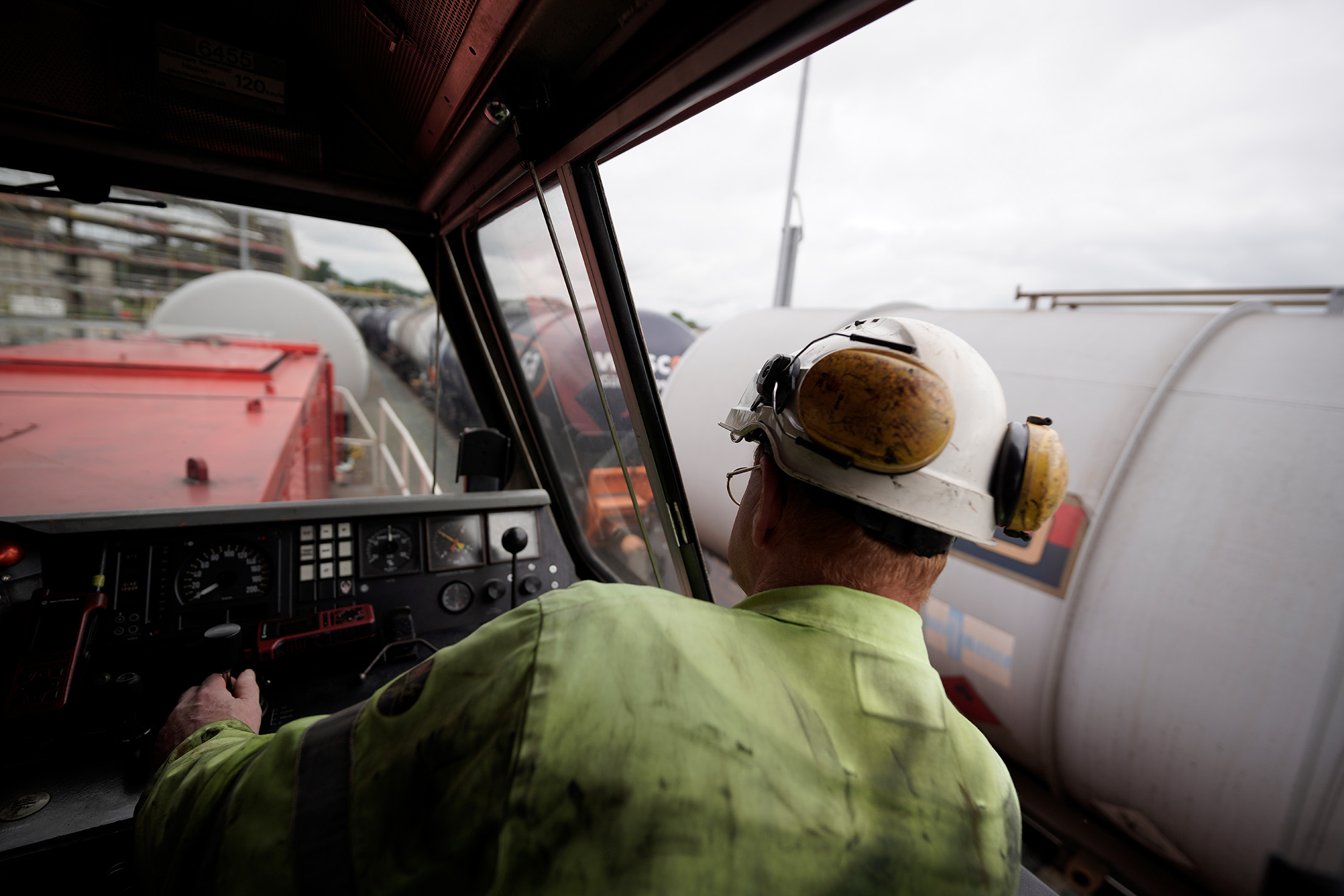
Goals
- Monitor and facilitate safe and secure transport.
- Demonstrate compliance with governmental regulations such as Basisnet.
- Route optimization and reduction of transportation and waiting times.
- Condition-based (preventative) maintenance: check-up dates planned in accordance with the tank container's actual mileage and registered wear and tear, instead of according to merely a pre-planned schedule.
- Measure the performance of logistics service providers and provide corrective feedback to maintain the best in class supply chain.
- Enhance customer Service by monitoring and pro-active information about the status of transports.
Process and highlights
AnQore defined a road map with 4 major phases to implement sensor technology including a governance structure for monitoring and continuous improvement. We started in 2019 with the system selection and introduction. We connected the software to our ERP system and started to review basic reporting. During the second phase we improved the system with our software partner. At the end of 2021 we connect external partners and add sensors to measure more things, like exact volumes and temperature. Lastly, we embark on a journey of continuous improvement to enhance the system and unburden customers, our own organisation and help improve our logistics partners.
Originally a project team was set up with a mix of functions and expertise involved, like IT specialists, Customer Service employees, Sales Managers, Logistics specialists and external support from our partner in sensor technology, Savvy. Weekly project meetings with Savvy were instigated to track progress, and bi-weekly meetings were held with the team.
Especially the Basisnet compliance report was a challenging exercise. Basisnet is a Dutch system to govern the transportation of dangerous goods via rail, road and water. For more information please visit “Basisnet - Kenniscentrum InfoMil AnQore needs to make sure that all our transport meets the criteria of Basisnet. To help us in making our transport history clear and insightful to the Dutch department of transport we decided to design a bespoke monitoring report. We started to map the rail network. In our system the rail network is displayed via geofences, but as the GPS devices only share their position with a defined frequency. This didn’t work at first how we intended and required some fine tuning. Shipments can now be monitored in real-time. Processes can be coordinated with customers and logistics partners more efficiently. We have shared our reporting with the Dutch ministry and it has been used as an example of best practice for others.
As a result of the completed roll-out in March 2020, all sales and customer service representatives are now using the SAVVY® Synergy Enterprise portal enabling them to track the whereabouts of all AnQore equipment real time and advise customers on the location of railcars, expected arrival times and OTIF reporting.
Results so far
Objective |
How it is effected |
Monitor and facilitate safe and secure transport. |
|
Demonstrate compliance with governmental regulations such as Basisnet.
|
|
Route optimization and reduction of waiting times.
|
|
Condition-based (preventative) maintenance
|
|
All in all we are convinced that we have made the transport of our products much safer and have laid the foundations for many value add services for our customers and partners.